Werlcome! to the most advance steel rolling mill of North India
We are sharing our production process so that you can understand about how the product you are buying is made. Sharing knowledge is the most important aspect of any work.
Raw Material Procurement
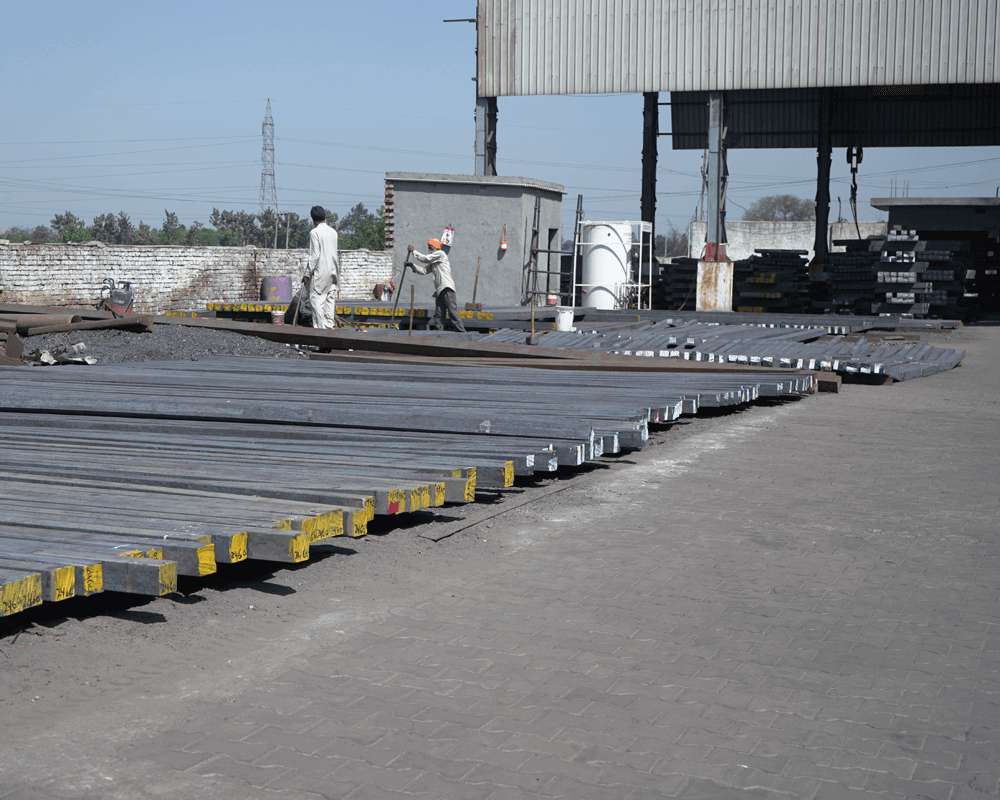
Our raw material (Billet/Ingot) is procured from Bhawani Industries Pvt. Ltd., a group concern of Royal Group. Rew material is transfered from furnaces to our premises heat wise attached with test report through truck. Billet arrives to our premises in the length of 6 meter and then splited according to desired size for making desired length, so that we can make proper cut leanth material wich saves the rejections. Colour code is given as per grade to segregate and for easy traceability. Raw Material is then checked (Physical as well as lab) for any defects. if any defects are found we segregate it and is returend to the furnace.
Reheating Furnace
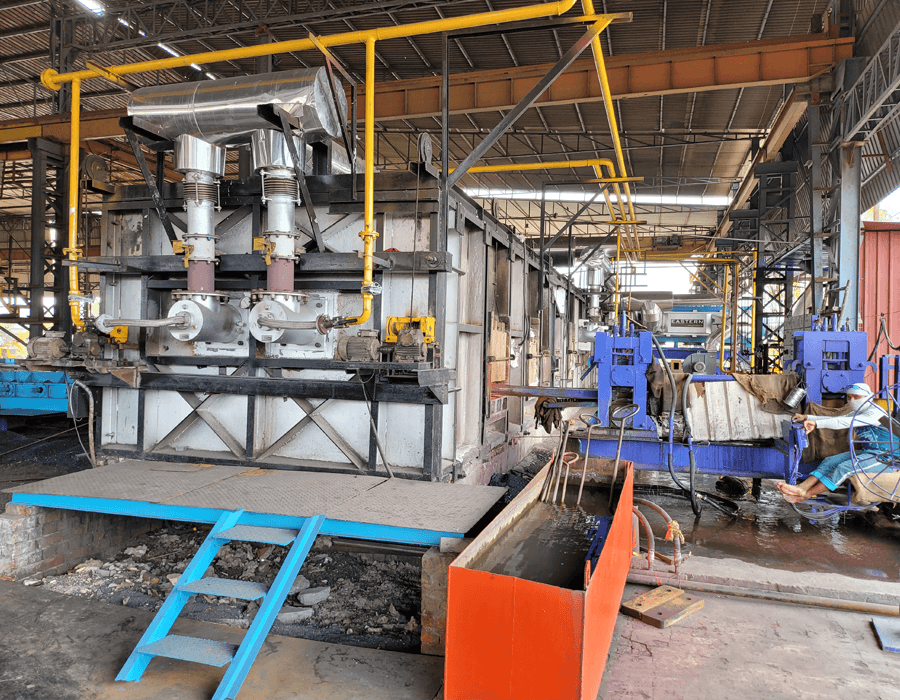
Billet is then feeded to reheating furnace. Under proper supervision of qualified supervisors who are their to ensure lots are being feeded heat wise in the furnace so that there is no mistake feeding. Temperature inside furnace is controlled by automatic drive system as per the required heat for a size and is controlled by expertized trained fireman. Furnace leanght is 25 meter long single line which help to maintain temperature upto 1300 °c. Our furnace capacity is 15 ton per hour.
Roughing Stand
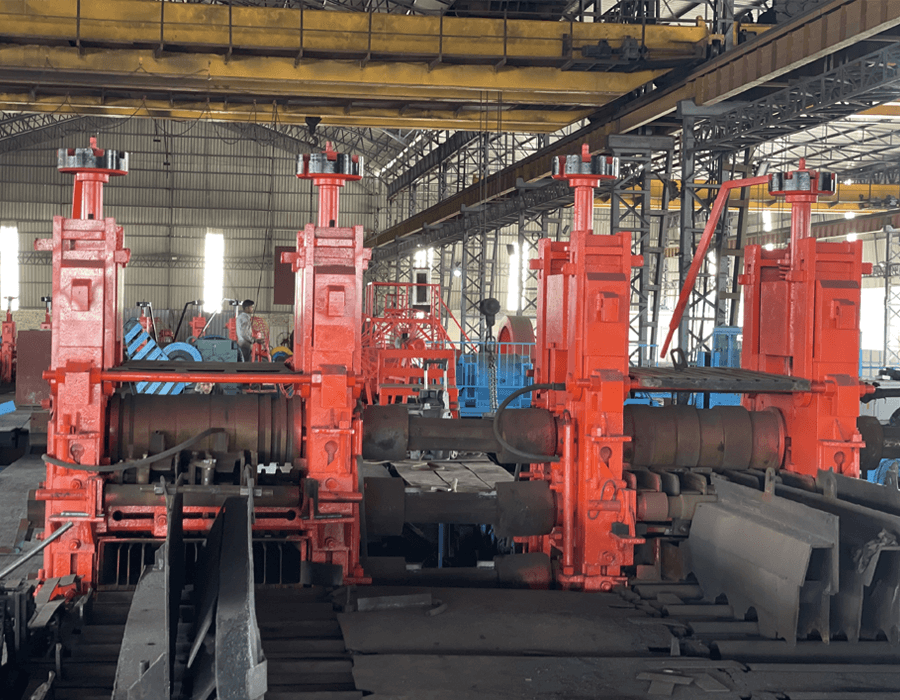
Material when is heated then is transferred from furnace to roughing stands. The hot billet is then passed through roughing stands. 2 number of 18” 3 high rolling stands are installed from which we pass 7-9 time zig-zag moment of billet compressing it to desired size. We can roll flat size 40 x 5 mm from 160 x160 mm billet section which has been highest reduction ratio.
Rolling Mill Rolls
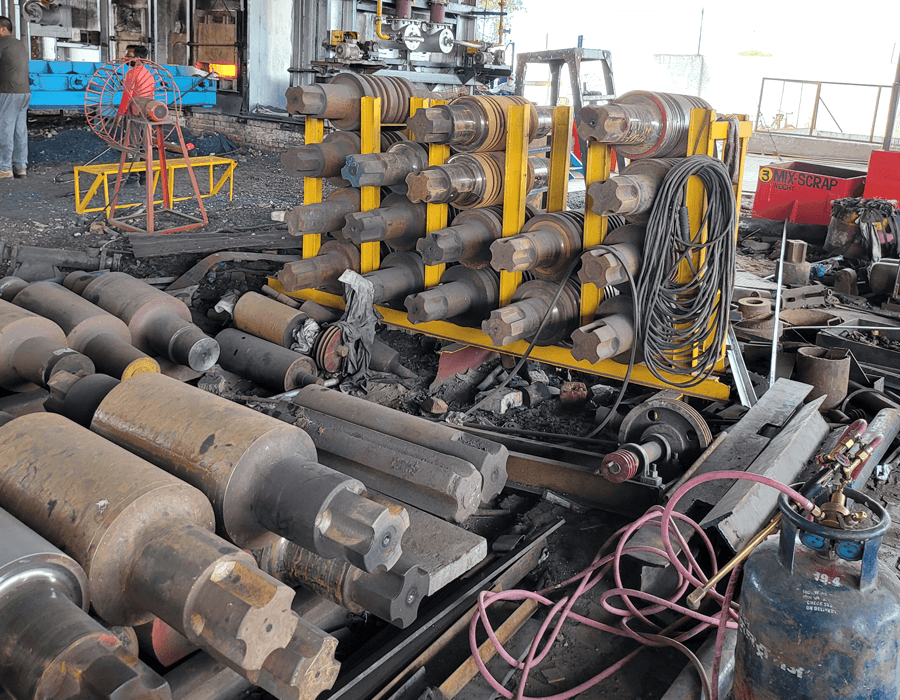
Rolls adjacent shown are high grade used which help us to roll the material in the mill stand different set of rolls are their for different sections we have stock of triple sets of rolls for each different sections in our inventory so that our production don't suffer and also there is no problem in quality. Rolls life has been set to a particular number of production to be produce after that we scrap the rolls. We have up to date machinery for turning and for polishing the roll. Qualified trained people are appointed in the workshop who always ensures that the finish on the roll is as per the standards. There are specified rules mentioned which they follow.
Finishing Stands
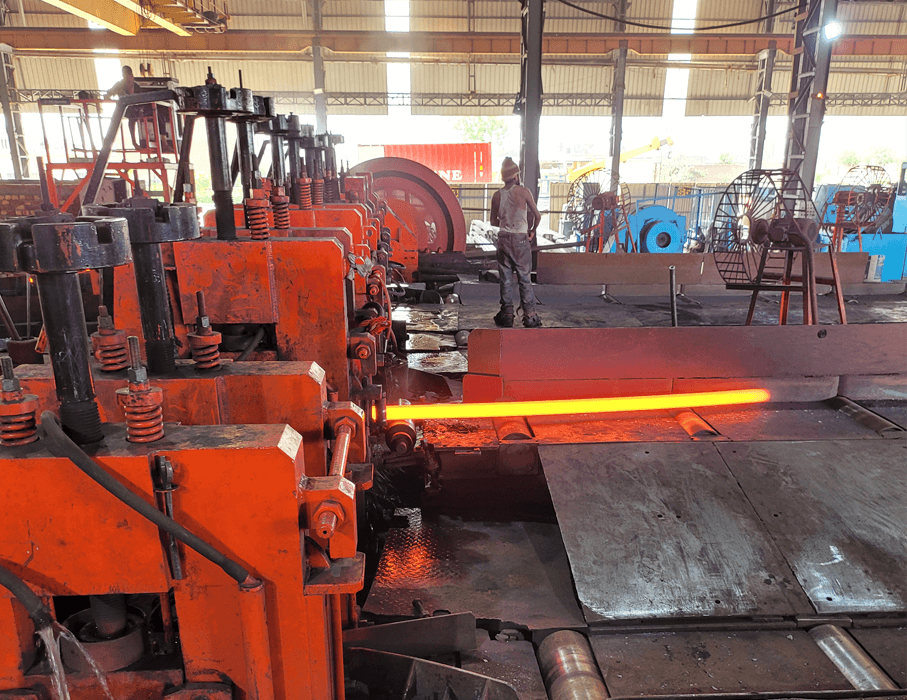
After roughing stand the material is then transferred through conveyor system to Finishing stand section. we have 7 horizontally lined 2 high rolling mill stand of 12”. For each stand different grade of rolls are used to roll the material. Material is then one by one single passed through each stand compressing it to desired size. A team of highly professional workers are appointed to ensure that we attain high quality of hot rolled flats as per accurate size and standard. The radius is maintained over passing through material by vertically in the stand. The rolls are checked trough all time of production so that if any problem is there in the material we can change the rolls. Shearing machine has been installed in the production line which help us to take samples in between of productions. Edges are shear down so that we can check the size of the flat to ensure the flat rolling is of proper size. A system is created for production process we have a quality norms in which every month we check the leveling of our machines. The maintainace is regullarly followed to ensure there is no breakdown during rolling process. Capicity of our rolling mill help us to roll 12 to 15 ton material in one hour.
Automatic Cooling Bed
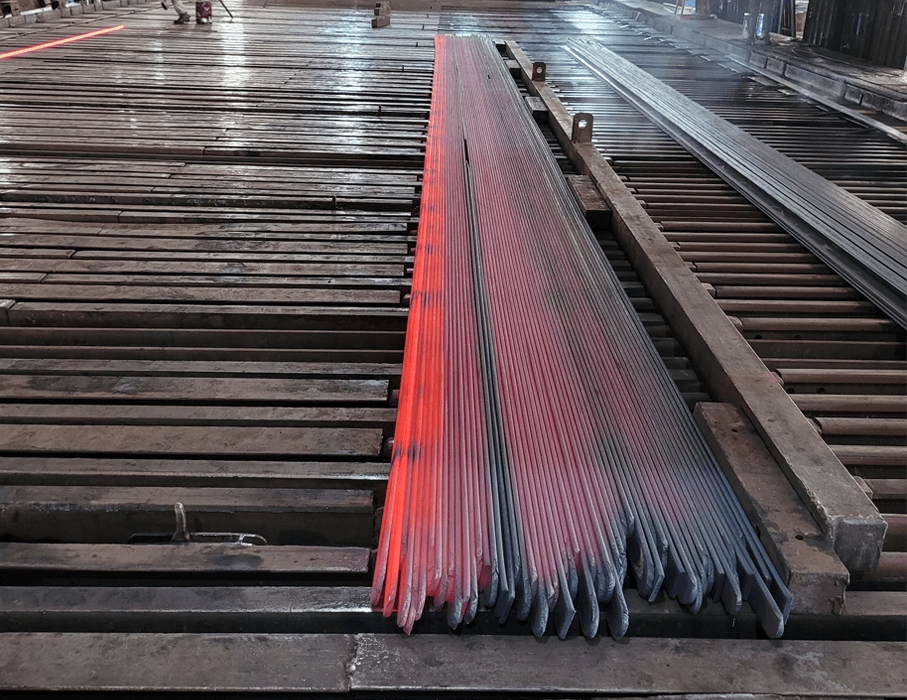
We have installed casted lines for support and the material is dragged through dock system one above one the material is stacked for slow cooling to attain proper hardness. Total 50 ton material can be stacked on cooling bed the casting rails help to make straightness of material. Our cooling bed is 30 metre long installed in a proper level and is fully covered from sides so that material cools down slowly. The material is then transfered to the inspection yard.
Inspection Yard
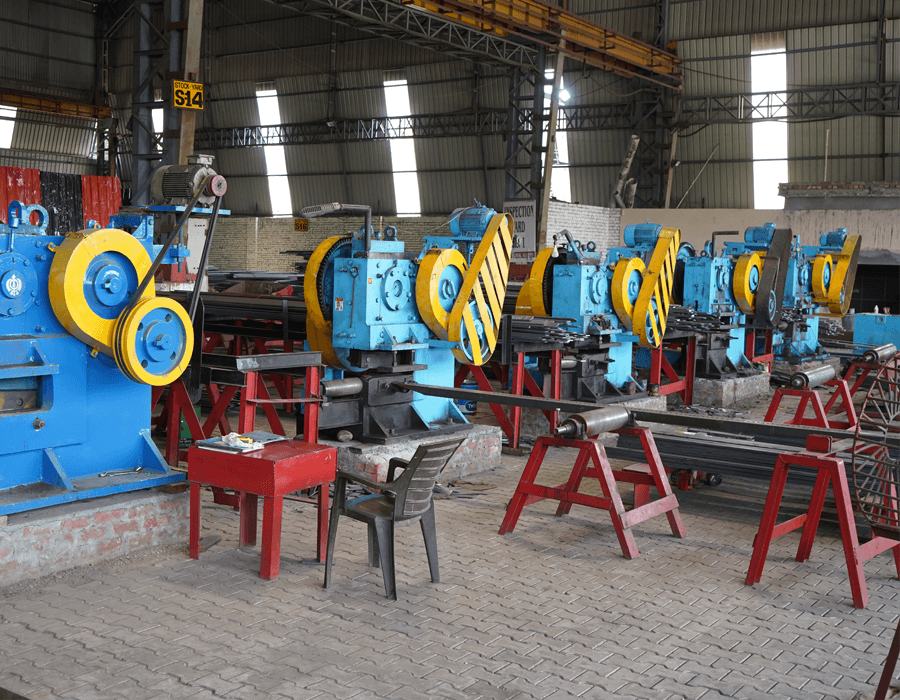
When flat is cooled it is cut down in half to be easily transfer and sent to inspection yard where the supervisor is been appointed to check the flat size, rolling defects and surface defect in every single pcs. Over inspection yard we cut the edges of the flat and also cut the flat by the desired size or as per customer requirement.
Bundling, Taging & Storing
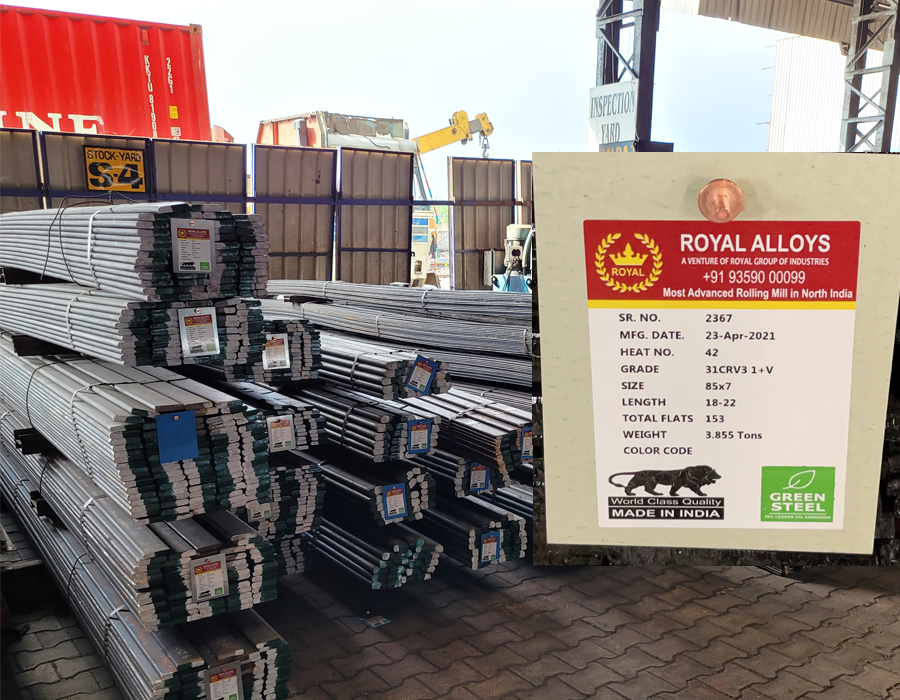
After inspection flats are bundled properly with steel strips and clumped.
Each bundle
has following information on it:
- Heat number is written as per the billet heat number for test report and traceability
- Size & Grade name is written upon these bundles
- Number of flats is written on the bundle
- Paint on edges is done according to the grade or as per customer requirement.
- Bundle is then transferred to the stock yard as per size or as per grade we keep into our stock yard section wise. Before loading into container or truck we wrap the bundle by plastic sheet on both edges so that moisture does not make red from edges.
Loading Process & Billing
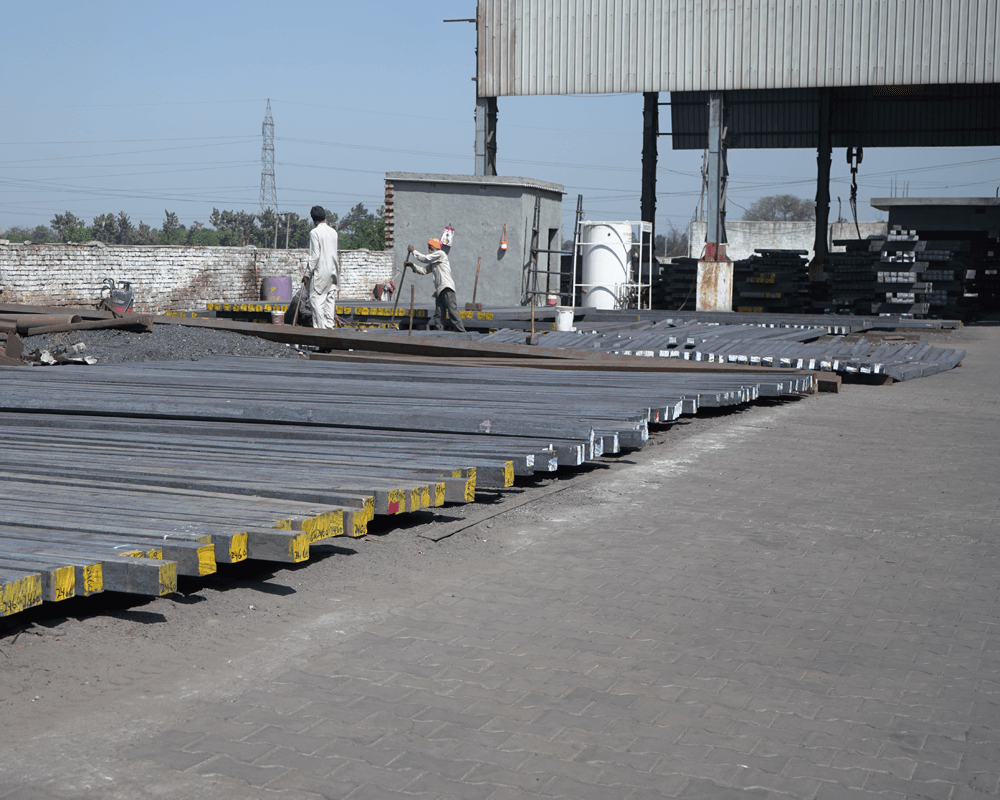
After the arrival of truck or Container material is then loaded in the truck according to size ordered by the customer and after weight we process the paper work which includes:
- Sale invoice.
- Mill test report is made according to the heat number written on bundle the test report is of our in house mill spectro report.
- Material origin test report is also provided from our billet plant Bhawani Industries Pvt. Ltd.
- Weight slip of the material loaded in the truck.